The protagonist
The Lean approach to the Italian winemaking tradition: the case of Mondodelvino
The story of Mondodelvino begins in 1991, thanks to the pioneering vision of Alfeo Martini (see photo on the left), Roger Gabb and Christoph Mack, enologists and wine experts who, together, established the MGM Mondo del Vino winery in Forlì. Since then, there have been three decades of growth and success for a company that has always been ahead of the trends, creating a business model marked by the combination of innovation and loyalty to the local lands. It distinguishes itself for the prestigious and high-end products it has to offer, for its dedication to the winemaking culture and local development, and for having built state-of-the-art facilities that are proof of commitment to innovation and sustainability. With a yearly turnover of 130 million euros, Mondodelvino is among Italy's top 20 winemakers, producing roughly 50 million bottles per year that are exported in over 55 countries around the world, in particular Canada, the United States and Northern Europe.
The challenge
4.0 data collection, smart production
In order to embrace the new approach and resolve the difficulties encountered, Mondodelvino chose to rely on the NET@PRO technology designed by Qualitas Informatica as an essential component of production data collection and for real-time maintenance and performance control. Thanks to the implemented MES, the team led by Marco Arduino, Mondodelvino Head of Continuous Improvement, General Services and Maintenance, was first of all able to assess and understand a series of unnoticed and past critical issues which, though apparently minute, constituted in effect a sizeable portion of production variables that were evading detection. The chunk of data collection that was managed manually has been largely reduced, thus achieving a reduction in the number of human-resource hours required to finalize production data by 66%, while also eliminating much of the paper documentation circulating in the production department and the development of a paperless system.
Integrated management system
In addition to streamlining production data collection and performance control, NET@PRO encompasses, and optimizes, equipment and machinery maintenance management by automating planning and finalizing. In particular, the system makes it possible to define a maintenance plan for every machine, indicating all the necessary activities and their frequency. With NET@PRO, even maintenance data becomes part of the company's digital assets thus guaranteeing, thanks to integration with production data, real-time detection of the causes of possible issues and the automatic generation of requests for maintenance work. In this way, machine downtimes have dropped by 30%.
The project
Lean Approach: to eliminate waste and inefficiencies
The Group's vision can be summed up in the offering not only of a quality a product but one that is also safe and right, with the aim of satisfying an international market and, at the same time, improving the Italian wine tradition by continuing a thirty-year practice of asserting identity, territorial and cultural values. In order to maintain and strengthen its presence on the international market, for Mondodelvino greater flexibility in the packaging customization offered became a necessity, which led to the introduction of approximately 1,500 references in the catalogue and various production lines. An ambitious goal that, considering the tremendous growth of the volumes, created many challenges for the Mondodelvino Continuous Improvement and Maintenance team, which decided to apply the Lean approach in the company production processes.
The application of this philosophy, which aims for the radical reduction of waste and inefficiencies combined with the development of low-cost, optimized standardized processes, had led to an overall rethinking of production data collection and to the need for advanced maintenance management. Indeed, the manual paper-based system in use, in addition to forcing the company to inefficiently allocate human resources, did not allow mapping of total work time or collection and organization of all the data in a timely and precise manner, thus giving way to a high margin of error and missing information that created a so-called “gray area.” There were many paper registers present in various production departments for use in processes or certification, and every new activity generated the need to create, compile, manage, and file paper forms, including machine and equipment maintenance requests, without outlining a historical archive of maintenance work carried out and the issues detected.
The benefits in numbers:
66% Reduction in the number of production data finalizing human-resource hours
90% Reduction in paper documentation
30% Reduction in machine downtimes
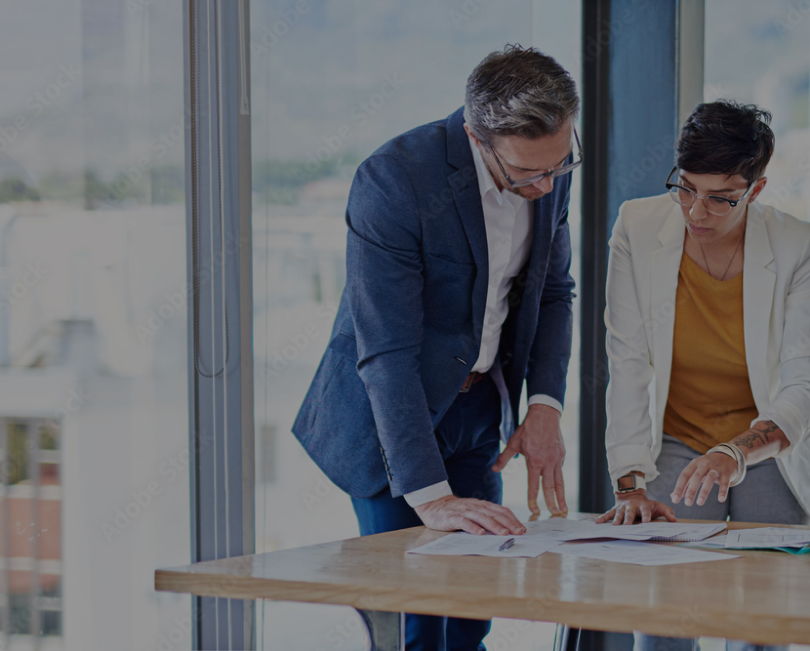
discover our connected services
.png?width=810&height=651&name=Rectangle%2067%20(1).png)